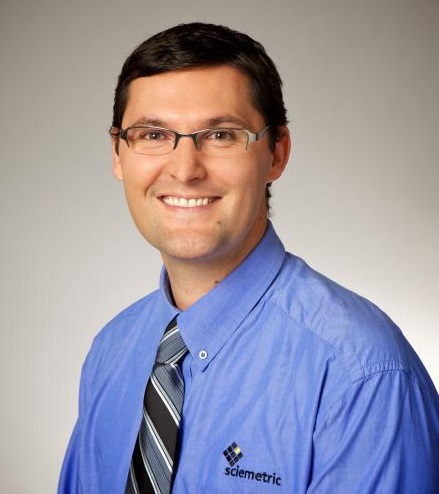
Contributed by: Ron Pawulski - Account Manager

A common quality issue at the weld station on a production line is expulsion – an unwanted ejection of molten material beyond the weld zone that can result in a weak weld joint. An expulsion is typically the result of overheated and rapid expansion of metal during the welding process.
Battery failures drive up warranty claims
Weld expulsions and other joining defects can lead to weak connections between surfaces. One example of this that we encounter on the production line is in the manufacturing of batteries, commonly used with internal combustion engines.
Inside the casing of a battery is a collection of cells. Each cell includes a series of positive and negative lead plates (with separators to prevent them from shorting out) that store the electrical energy.
The cells are connected by welded links. These intercell welds are key to ensure the battery delivers peak performance and achieves its expected operating life. A weak inter-cell weld leads to poorer service life and efficiency. Engine vibration, bumps and potholes will all conspire to make a weak weld fail.
We worked with one manufacturer as it investigated the causes of warranty claims related to poor-performing batteries. The issue was quickly traced to expulsions at the weld station. How could we catch an expulsion as it happened, to avoid shipping a bad battery?
Adding intelligence to the station to capture the right data
End-of-line testing by cycling each battery was not an option. The time required would have demanded dozens of test stations be set up and staffed to keep pace with production.
During the welding process, there are a number of feature checks we in can analyze in real-time, using the right sensors in combination with digital process signature analysis. These include voltage vs. time, current vs. time, force vs. time, distance vs. time, electrical power vs. time, resistance vs. time and force vs. distance. Together, they provide a complete view of everything that happened through every millisecond of a weld process.
We deployed sensors at this manufacturer’s weld station, paired with custom algorithms, to capture these feature checks. With digital process signature analysis, we discovered that the majority of expulsions cause a significant spike on that voltage vs. time curve.
We also added an accelerometer to the station. Why? Using the process data, we identified that some expulsions that could result in a weak weld were not great enough to cause a noticeable voltage spike. They did, however, cause a vibration across the weld jaws that clamp down before the weld operation. By adding the means to monitor for this additional feature check, we could also catch borderline cases that might only cause issues after many hours of cycling.
More advanced defect detection…without rip-and-replace
Digital sensors and analytics can be applied in this fashion to any existing process or test station to improve defect detection, overall quality and first-time yield. We can do this without disrupting the production line or requiring any costly rip and replace of equipment.
The more data you can collect and analyze from a process or test, the easier it becomes to understand what anomalies to watch for and what they signify. This enables more accurate and reliable pass/fail results in real-time, as well as predictive station maintenance.
Contact us to discuss how Sciemetric’s defect detection solutions could benefit your production line.
Learn more about using digital process signatures, including how to:
- Use process signature data to derive key insights
- Achieve better defect detection
- Set more effective limits
- Optimize test cycle times
- Adapt and adjust, quickly
- Continuously improve the production line