Contributed by: Rob Plumridge
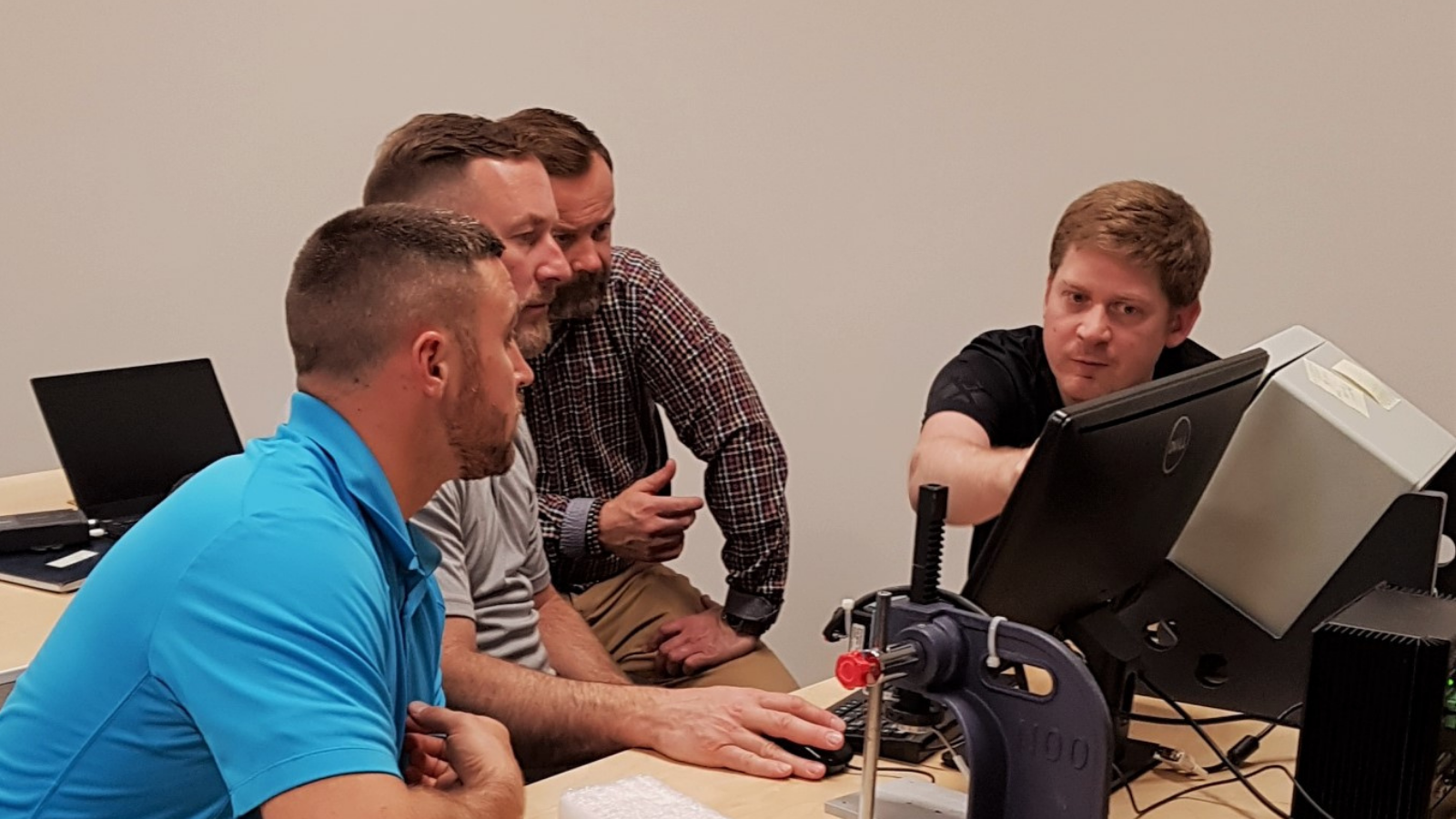
In our discussions with prospects about collecting and analysing part production data to drive quality and efficiency on a line, we sometimes get the question: “Why is it not enough to simply focus on machine data?”
I take that to mean, “Why isn’t it enough to focus on overall equipment effectiveness (OEE) values versus specific part data?”
The short answer is that both are important, and both have their role to play. But one is not a substitute for the other because they don’t measure the same things.
Machine Data Systems
At its simplest, an OEE system monitors machines to predict issues before downtime occurs. OEE is a useful tool for managing the health of a machine, managing its maintenance schedule and getting to the root cause of a problem. What it doesn’t do is directly monitor the quality of the part being produced by the machine.
If we are talking about OEE, we may as well address MES. Manufacturing Execution Systems deliver a more comprehensive focus on manufacturing processes and efficiencies than OEE by capturing data related to machines and people in product quality and throughput. A typical MES system tracks and documents the transformation of raw materials to finished goods with the goal to understand how current conditions on the plant floor can be optimized to improve production output.
And then we have Statistical Process Control (SPC). These systems and the data they collect can feed into an SPC system. SPC uses scalar data and statistical tools to monitor trends in production parameters to spot deviations that may eventually result in rejects.
And let’s not forget Operational Historians. Many plants also rely on process data that is time based, instead of tracked by the serial number of the part or assembly in production, using database software applications called ‘operational historians’. Historians record trends and historical information about industrial processes for future reference. They capture plant management information about production status, performance monitoring, quality assurance, tracking, birth history and product delivery.
The Shortfalls of OEE, MES, SPC, and Operational Historians
All these methods remain important tools for monitoring the health of a production line to spot issues as they arise. But this is what they don’t do:
- Provide direct insight into what is happening to a part in production, through every millisecond of its production, in real-time.
- Because they don’t, quality personnel lack the means to “capture at creation” a flaw or defect. Instead, the flawed part continues down the production line. The further from its point of origin a flaw gets before it is caught, the more costly it will be to address.
- Provide insight on how to improve a process. They only flag a problem, without providing the intelligence to quickly enact a fix.
Directly monitoring the results of a process or test on the line by directly capturing and visualizing the part production data with digital process signature analysis, on the other hand, enables all these things.
Digital process signatures deliver the part data and insights into quality that you need to be proactive
Consider it this way – OEE and these other measures of manufacturing performance are largely reactive. By the time a problem is flagged, flawed parts have already slipped through. The available data seldom provides a precise way to identify and quarantine flawed parts without also sidelining good ones.
Compared to these other popular data systems, digital process signature analysis is far more proactive. It can reduce, often dramatically so, the severity of a quality issue by flagging it as close to its point of creation as possible, as soon as possible.
Want to learn how digital process signature analysis could be employed to improve quality and efficiency at your plant, saving you time and money? Contact us!