Contributed by: Rob Plumridge
A chief goal when it comes to optimizing any leak test is to ensure if the cycle time of the test can keep up with the pace of production. This prevents the leak test station from becoming a bottleneck on the line and avoids the cost of having to deploy and staff a parallel test station.
One factor in optimizing the test so that it can cycle as many parts as quickly as possible with an acceptable range of repeatability and reliability is test pressure. Consider the following factors when identifying proper test pressure for your leak test.
Physical limitations
The physical limitations of the part may dictate a maximum test pressure to avoid damage. If the part being tested has fragile components, be sure to take this into consideration.
Type of seals: Lip seals vs. O-rings
Another consideration is the design of any seals in the part. In practice, lip seal defects will be exposed with a low-pressure test, while an O-ring seal will require higher test pressures to show a defect. This relation is due to the physical design of the seal, where high test pressures can actually cause a lip seal to deform allowing it to seal, while an O-ring at low pressures is able to seal due to the mating force preload at the joint it is sealing, causing a false pass.
Avoid the allure of too-high test pressures
Many operators and engineers may lean towards higher test pressures thinking they are most effective at finding very small leaks. However, higher pressure will mean more air needs to enter a part which can lengthen the fill time and also cause a greater temperature gain.
Increased fill time and temperature gain can consequently lengthen the stabilization phase of the test and make the part more sensitive to temperature fluctuations in the vicinity of the test station and in the part itself.
Even if there is no risk of damage, high pressure can still cause deformations that can affect the part’s dimensional stability during the test, which could mask other leaks or cause a false fail.
Test fixtures can also be negatively affected by higher test pressures:
- The higher stress can shorten the lifetime of a test seal
- Part fixtures may be deformed by the high forces exerted on seal faces, resulting in repeatability issues
- Higher pressure tests can pose a safety risk to operators. This may require special guarding and safety procedures to contain the large amount of stored energy that is present inside the test part.
So, what’s the best approach?
The best approach really depends on your specific part and setup. To identify the ideal test pressure, run a series of tests at multiple test pressures with both passed and defective parts. Analyze the data to gather statistical evidence as to the best test pressure.
If all data gives similar results, then the lowest test pressure possible is recommended. In addition to faster cycle times, the lower pressure and leak rate will support higher sensor resolution, offering the best possible repeatability.
Looking to use data to analyze your leak test?
Download our free e-book!
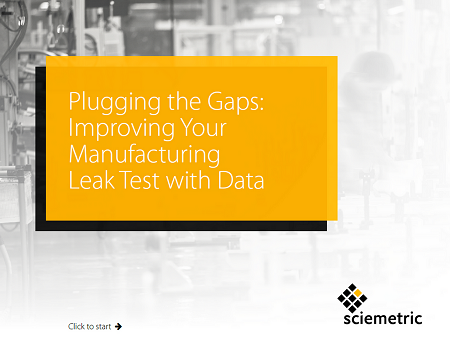
In this e-book, we explain:
- What is the right data to collect
- What a waveform can tell you
- What you can do with leak test data
- How Sciemetric is helping manufacturers improve their leak test with data...and how we can help you do the same