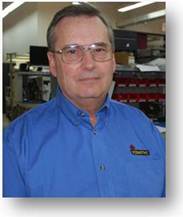
Contributed by: John Perkins - Senior Technical Support Specialist (Retired)
John Perkins is a manufacturing applications expert who has built hundreds of applications to help improve production and part quality. Though John is now retired, we can still answer any questions you may have at inquiries@sciemetric.com.
Question:
Dear John,
What’s the difference between a pressure decay leak test and a flow-based leak test? How do I know which one I should use?
Answer:
Leak testing is one of those things that is more complicated than it seems on the surface. The differences between pressure decay and mass air flow will illustrate this quite nicely. Let’s start by giving a quick overview of both types of leak tests.
In pressure decay, the part under test is pressurized (i.e. filled with air until it reaches a set pressure), then isolated from the supply pressure. The pressure within the part is then monitored using a pressure sensor, and as the air leaks out, the pressure drops. The leak rate can then be calculated based on the change in pressure over a certain period of time. In mass air flow, the part is also pressurized, but in this case the part remains connected to the supply pressure. Once an equilibrium is reached and the pressure inside the part is stabilized, the amount of gas flowing in from the supply must be equal to the total leakage of gas out of the part. In this case the leak “rate” is measured directly and no conversion is necessary.
So which approach should you use? Well, that all depends on the application. The advantage of the pressure decay method is that it is sensitive to very small leaks. It is also the simplest of the leak test methodologies and is therefore generally the least expensive to implement. However this test must be carefully calibrated against an accurate leak standard, and the calibration is dependent on the volume of the part under test. So if you’re going to be testing many different sized parts at the same station, this will become a challenge to manage.
One of the key advantages of mass air flow is that it is relatively insensitive to changes in the part volume and does not need to be recalibrated if a larger, or smaller, part is tested. In fact it does not need to be calibrated against a leak standard at all – rather the leak rate is measured directly by the flow meter (of course, the flow meter does need to be calibrated from time to time, as any measurement device does). This makes it particularly well suited to applications where different part types or tests are performed at the same station, or where there is significant variation in volume from part to part.
Mass air flow does it have its own set of issues to deal with. Because the part remains connected to the supply pressure throughout the test, it is sensitive to fluctuations in supply pressure. It is also more difficult to make accurate measurements at very low flow rates, making it less suitable for very low leak rates or very small volumes. Finally, because it requires both a pressure sensor and a flow meter (pressure decay requires only a pressure sensor), additional valves and filters, it is generally more expensive to implement than pressure decay.
So, clear as mud, right? Let’s put it this way. If the leak rate is small, pressure decay is probably the best solution. If the volume varies from part to part or if a variety of parts are tested on the same tester, mass air flow is probably the way to go. Another factor to consider will be cost, which favours pressure decay. Both techniques can provide accurate leak rate measurements, but clearly there are a number of factors to consider before deciding which one is the right fit for your application.
Now that we’ve cleared that up, I should point out that regardless of whether you have chosen to use pressure decay or mass air flow, there are still a number of other considerations that you will need to take into account before you can finalize on a leak test solution. For instance, the test pressure requirements, cycle time limitations, repeatability (i.e. Gage R&R) targets, and perhaps most importantly, the temperature sensitivity of the part and the test environment, will all factor into the configuration and test procedure that will best suit your application. Unfortunately, as these factors all tend to interact, it is difficult to provide simple guidelines on what will work best for you. The best advice I can give you is to examine the entire leak test signature, not just the maximum leak rate, to determine if your test is providing accurate and repeatable results. To do this you will need to select a test system that records the pressure and/or mass flow rate throughout the entire test cycle, including the fill, stabilization and leak/decay measurement phases.
Like I said at the beginning: leak testing is not as simple as it may seem.
This article features screenshot's from Sciemetric's sigPOD, learn more about the sigPOD's capabilities.