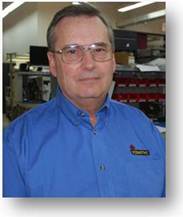
Contributed by: John Perkins - Senior Technical Support Specialist (Retired)
John Perkins is a manufacturing applications expert who has built hundreds of applications to help improve production and part quality. Though John is now retired, we can still answer any questions you may have at inquiries@sciemetric.com.
Question:
Dear John,
Now that I’ve collected all this production and signature data, what can I do with it?
Answer:
That data is a goldmine, just waiting to be mined. Let’s start by looking at the pass/fail data, which can be translated into yields. Comparing the yields across stations allows you to identify the ones that are underperforming and in need of some attention. Then if you trend the yields over time, you’ll be able to look for negative trends that indicate something is adrift. Now you can catch small problems before they become big ones. In both cases, proactively tracking your yield data allows you to increase and then maintain your production yields.
Now let’s dig a little deeper. Identifying which stations have the poorest yields is really just the first step. To improve the yield requires an understanding of why it is low. The answer is usually right there in the data. You can start by looking at the trends and histograms to see if the failures are grouped together or share some common characteristics. Are there any correlations to upstream test results or component data? Then take a closer look at the raw test data. Are there features in the process signatures that are only present in the failed parts? These types of clues can often be quickly traced back to the process error, sub-component defect, or operator error that led to the problem. Based on your findings you can eliminate the root cause, and introduce an additional feature check on your test stand to make sure that you’ll catch it if it happens again.
Finally, let’s consider this nightmarish scenario: you discover that some of those failed parts actually made it out of the building and are being found by your customers. Believe me when I say that if this should happen, you will be very relieved that you have all this data, because it will allow you to quickly identify which parts were affected. Now you can act quickly to address the situation without disrupting your entire customer base by issuing a mass recall.
Like I said at the beginning, your data is a gold mine, and I’ve really only scratched the surface of how it can save you money. The important thing is to start digging!