Contributed by: Jason Koval - Applications Engineer, Sciemetric
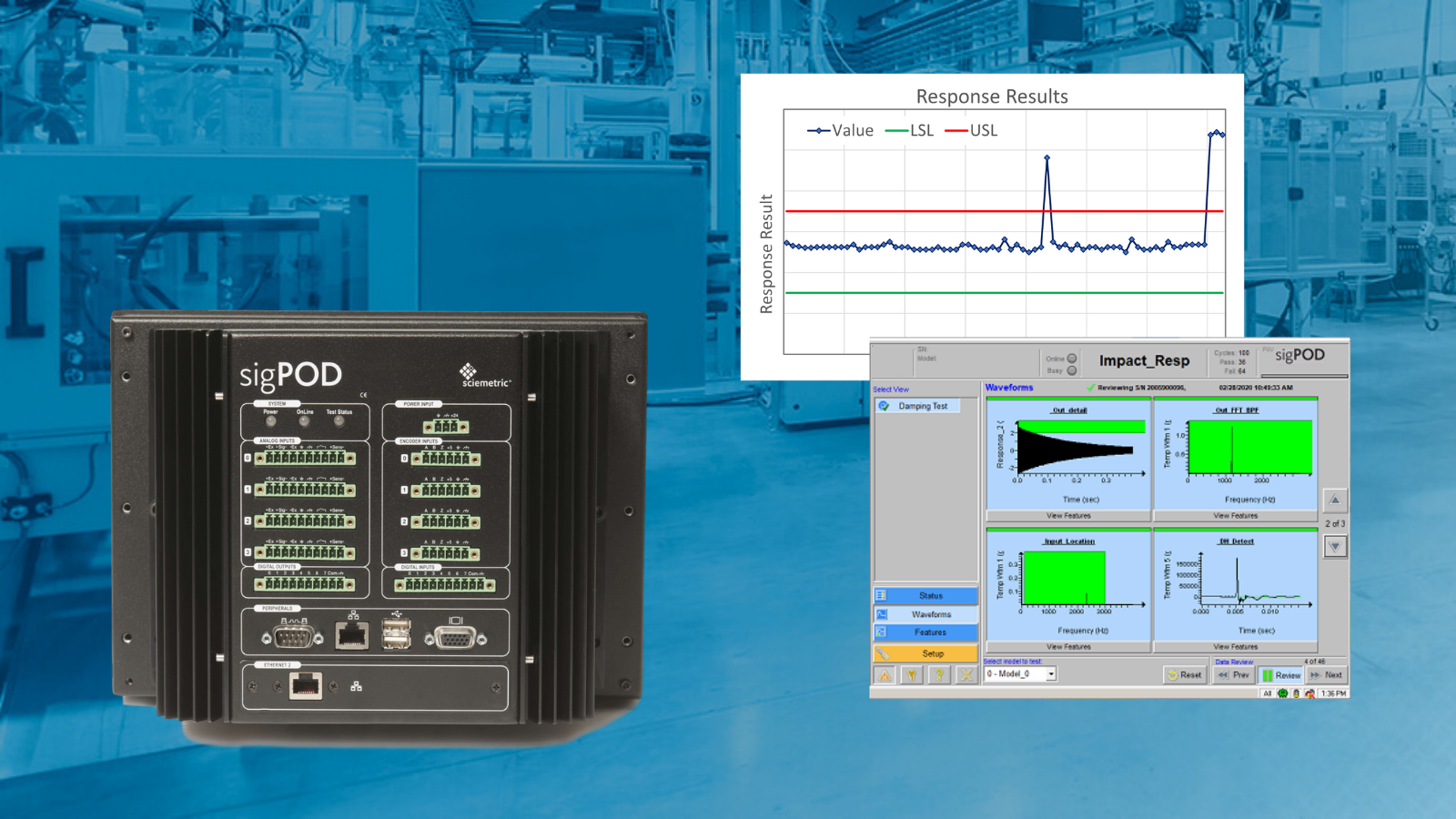
As any driver can attest, brake pads are a very important part of any automotive construction. The ramifications of faulty brake pads in the field are quite serious, making quality control very important. This starts with the manufacturing process.
Brake pads can be constructed of a variety of materials, which need to be securely bonded to a backing plate to function properly. Failure to ensure a proper bond between these materials can result in costly scrap and rework, not to mention loss of customer trust in your brand which can hurt the business even further in the long run.
Testing brake pads for delamination
In order to ensure a proper bond, you need a test in place. Simple visual inspection of the part isn’t going to cut it. This kind of quality control measure is most often evaluated using NVH (noise, vibration, harshness) testing, or more specifically with an impact response or “ding” test.
During this test, you essentially strike the brake pad with a method of force application. The resulting frequency is then recorded to determine the state of the bond. When it’s bonded perfectly, you will get a certain consistent frequency. If there is delamination happening, it will be demonstrated with a reduction in the sharpness of the characteristic frequency peak with indicates the increase in structural damping due to the delamination. In layman’s terms, the characteristic frequency doesn’t continue to “ring” as long as a properly bonded part.
While there are a variety of systems on the market for this kind of impact response testing. Many rely on complex mathematics to analyze the Frequency Response Function (FRF). In my long-time experience in NVH testing, these solutions work great but usually they cost more than a manufacturing facility is willing to spend or the overall NVH-based system solution is overkill for the application.
Sciemetric’s solution, however, eliminates the need for complex mathematics and complicated systems that are difficult or costly to maintain. I’m always excited to show this solution to manufacturers as a more efficient and cost-effective solution.
Let me use a recent customer story as an example of how Sciemetric can help you effectively detect delamination of brake pads using impact response testing.
Manufacturer’s manual brake pad quality checks proved ineffective
A manufacturer of brake pads had been getting returns in the field from their OEMs. Complaints about reduced reliability and durability was becoming a problem, both financially and for their reputation with their customers. After some investigation, they found that the problem was delamination of the friction materials in their product.
They realized their manual inspections were not providing effective quality control and putting their business in jeopardy. They needed a reliable way to detect delaminated layers thus ensuring secure bonds before the product left the plant. They turned to Sciemetric.
Sciemetric’s solution for automated impact response testing
To deliver on the manufacturer’s needs, we enlisted the Sciemetric sigPOD.
With the sigPOD and its user-configurable PSV™ (Process Signature Verification) software, an application was created to drive a solenoid-based impactor into the brake pad. We applied an automated solenoid impactor with the SigPOD’s on-board 5V excitation to keep the impacts consistent for better test accuracy—a key feature missing in many systems on the market.
The sigPOD was then set up to measure and record the impact and response vibrations, then calculate a response metric corresponding to the presence of delaminated area.
By analyzing the data created by known good parts, we were able to set effective limits for the test. Using these limits, the system was set up to issue pass-fail results and report them to a PLC, along with waveforms for review as desired.
This ability to plot your data using waveforms allowed the manufacturer to easily isolate their problems, which are displayed as visual outliers outside of your set limits (see image, right-top). Interestingly, when analyzing this graph, the first peak in the middle was due to a part among the population of “known good” parts being detected to have delamination. The value of the sigPOD system was proven immediately.
The system’s additional waveform analysis capabilities were employed to validate the input force, the sensor condition, and other parameters (see image, right-below).
In addition to simply detecting the delamination, Sciemetric’s solution also allowed the manufacturer to identify why the delamination was occurring by giving immediate feedback to the manufacturing team. For example, by analyzing the waveforms, it was apparent that there was contamination present when pad materials were bonded together. This informed the team to examine the bonding process and fix the problem, preventing the same issue from happening in the future.
In the end, the manufacturer achieved an accurate, repeatable, automated test to detect delamination of brake pads—all with a cost-effective solution. The use of the sigPOD’s excitation voltage and built-in logic outputs eliminated the need for an expensive NVH solution on the manufacturer’s line, solving the delamination detection problem simply and at low cost.