Contributed by: Sciemetric Staff
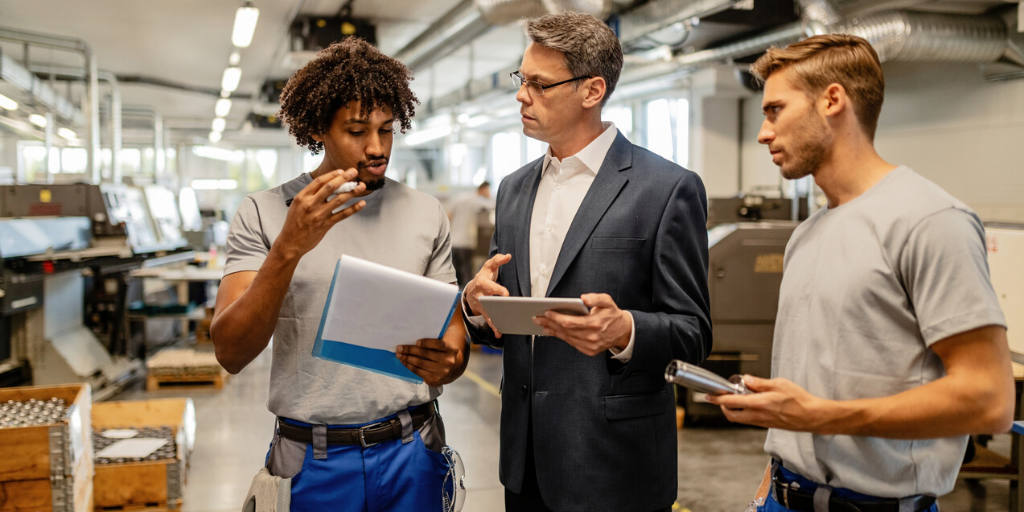
There has been plenty of talk through 2019 about how IIoT and Industry 4.0 technologies and advancements are going to change the manufacturing industry.
But instead of using new technologies to completely remake the way a plant or production line works, we prefer to focus our attention first on tangible problems that are impacting quality, yield or profitability.
We want to help manufacturers with these problems and look for ways these new ideas and technologies can start to be applied to see improvement on your line—without a massive overhaul.
What is that persistent problem you’re experiencing on the line? And what technologies are available and ready to deploy today that will address it? The answer often doesn’t have to require a widespread overhaul or disruptive change. Instead, incremental changes can add up to substantial improvements and provide manufacturers with a cost-effective way to ease into their Industry 4.0 transformation.
Here are some things to consider as you look at ways to improve your manufacturing line in 2020:
1) Don’t rely on the end of the line for defect detection
The quicker you can catch a defect, and the closer to its point of origin, the less costly it is to address and the less disruptive it will be to the production line as a whole.
While end-of-line testing plays a good role in verifying the reliable function of a completed assembly, relying on EOL testing alone can be costly, complex and often problematic if it’s your only process for defect detection. If a problem crops up at this point, the only recourse may be a costly teardown to trace the root cause with only educated guesswork to guide the process.
Meanwhile, the production line may be left idle while you try to identify the cause to avoid your other product being affected by the same problem—slowing production and affecting your bottom line.
Learn more about the benefits of in-process testing for defect detection in this post, “Why Relying on End-of-Line Testing is Bad for Your Bottom Line.”
2) Consider your options before ordering a rip and replace of your whole system
Many manufacturers are hesitant about updates to their process because they’re envisioning a deployment of a large, complicated enterprise system. But when it comes to deploying modern IIoT/I4.0 technologies, the deployment cycle doesn’t have to be massive and complex.
In fact, it can be measured in hours, characterized by small, manageable steps instead of giant leaps.
With today’s modular and additive technologies, it is relatively easy to install data collection and analysis capability onto problematic processes or stations and have it start yielding valuable insight to improve your line almost immediately.
Once you have proven the value of such an investment at one station, it’s easy to expand the deployment across the production line or the entire plant.
Learn more with our post, “Quality Assurance is Falling Short? Consider Retrofit Before a Rip-and-Replace.”
3) Make sure your critical stations are set up for success
Many manufacturers find that upstream production issues are often red-flagged at the leak test station—provided your test is accurate and reliable.
Making more effective use of data to improve the reliability and efficiency of any process and test station on the line is part and parcel with IIoT/I4.0. Leak test is the perfect candidate for this, considering how challenging of a test it can be to get right, even under ideal circumstances.
Modern digital sensors and electronics, coupled with the latest in data analytics, are only part of the answer. Despite this digital age, a better leak test begins with mechanical engineering – having the right fixturing and connections and test pressures.
For more on leak test, this post provides helpful tips: “Factors In Identifying Proper Test Pressure for Your Leak Test.”
4) Make smart use of the data available on your line
Sometimes the conversation around IIoT/I4.0 doesn’t quite drill down to the granular level that can be the most helpful for manufacturers—the part production data.
This is the data generated by a part in production from each process and test. Manufacturers are swamped by reams of it, but many have yet to understand and appreciate its utility and take full advantage of it.
Sciemetric believes in enabling deeper understanding of your part production process by capturing data in the way of digital process signatures from each cycle. A digital process signature is a visual representation of everything that happened through every millisecond of that manufacturing operation on a particular part.
Each combination of a part and a process is unique and the signature is repeatable and consistent when a process or a test cycle completes within its acceptable parameters. A signature that does not match the established norm indicates a flawed process and a defective part.
Learn more with our post, “Digital Process Signature Analysis: The First Step to Industry 4.0.”
5) Eliminate guesswork with your data
Process signature analysis helps in many ways to improve the efficiency, quality and yield of your line. Two great examples are how they can be used to accelerate how quickly you can establish the right limits for your tests, and how they can be used to carry out more extensive and accurate data analysis for continuous improvement.
Learning what your part production data can tell you through those process signatures is a highly effective way to begin your IIoT/I4.0 journey.
Learn more with our post, “Take the Guesswork Out of Finding Your Limits.”