Contributed by: Sciemetric Staff
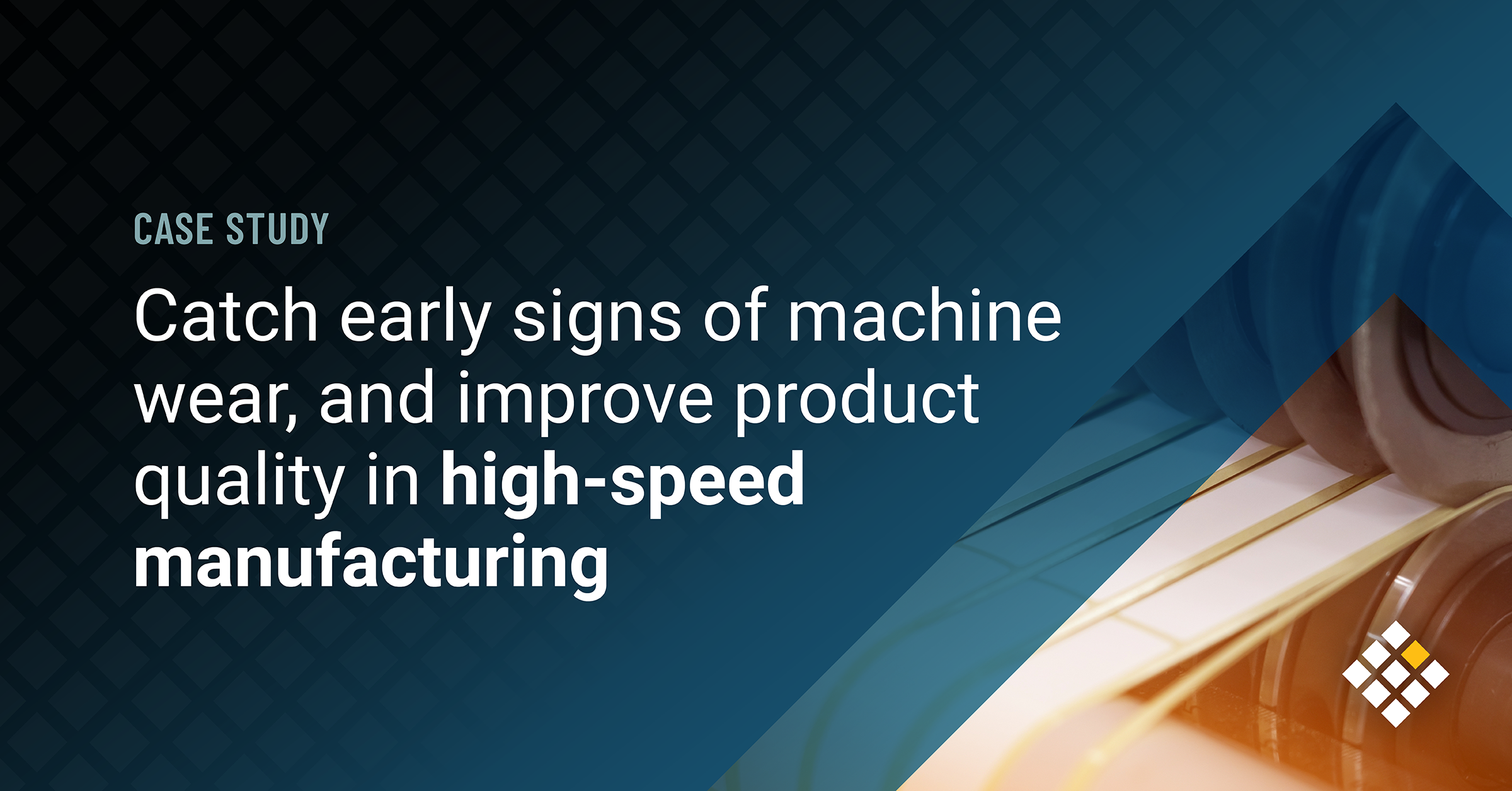
In applications where precision is key, maintaining perfect calibration and a properly functioning machine is critical to ensure product quality and avoid costly amounts of scrap and production downtime. This is even more important in a high-speed manufacturing environment.
Struggling with precision in a high-speed manufacturing environment
Sciemetric had one customer, a leading supplier of rotary cutting dies, that was struggling with the dependability, efficiency, and operating life of its products in the field.
Rotary die cutting is a high-speed and high-precision manufacturing process that is used for applications as diverse as labels, automotive components, and multi-layered parts. The material (which could be a thin metal, plastic, paper, foam, fabric or laminate) is drawn and pinched between a rotating cylinder that contains sharp cutting blades (the die) and a smooth cylinder rotating in the opposite direction (the anvil). The press, which houses the die and the anvil, can be calibrated to cut to depths as fine as the thickness of a sheet of paper.
Maintaining high-speed manufacturing processes with the highest degree of precision was of the utmost of importance for this manufacturer. In some scenarios, it could take only seconds for hundreds of feet of material to be wasted due to poor cuts if the clearance between the anvil and the die was too great or misaligned. They needed a reliable, accurate process monitoring system to catch defects and early wear problems with machines in real time.
Solution: Achieving high-speed, high-precision defect detection with Sciemetric’s sigPOD process monitoring system
The rotary die maker first deployed Sciemetric’s sigPOD on a setup designed to cut and shape plastic cup lids.
Load cells were placed strategically to measure the vertical force between the bearing blocks that support the die and anvil in the frame of the press. As the die and anvil rotate and sheet material was pulled through, the sigPOD captured the force applied during cutting to monitor machine wear, as well as any changes in the die’s alignment or clearance with the anvil during production.
The sigPOD, equipped with Sciemetric’s unique process signature verification technology, performed the calculation to gauge sensitivity. In this case, the load cells had a range of 10,000-lb full scale. The cutting force precision of interest was less than 1 lb—easily measured using the sigPOD.
Figure 1 (below) shows an example of the process signature visualization of the cutting force for the simple star-shaped cutter. Three cuts in fresh material are shown along with three runs without material. This process signature captures and displays the three cutting events clearly as the spike, distinguishing it from the 8,000-lb constant static load of the rotary die press.
Along with clearly indicating when/if contact was made, this measurement would also allow the manufacturer to discern if the die and the anvil were operating with too little clearance. This would cause harder physical contact (force) between the die and anvil than necessary, which could shorten the life of the press components and increase machinery maintenance and replacement costs for the end user customer.
In Figure 2 (below), the 14-lb cut is easily discerned. The repeatability shown, which could also be described as the degree of variance between cuts, is less than 0.5 lb for the three cutting events, well within the manufacturer’s required repeatability range.
Result: Cutting scrap and downtime leads to higher production yield, improved profitability, and efficiency for manufacturer
The sigPOD enabled continuous monitoring and reporting of machine performance in production real-time for true quality assurance. The ability to perform predictive maintenance on equipment also provided the added benefit of improved machine lifespan and decreased replacement costs.
By equipping its machines with data-driven process monitoring using Sciemetric’s sigPOD, this manufacturer was able to ensure the dependability, efficiency, and operating life of its products in the field, securing them an impressive competitive edge in the market.
Interested how the sigPOD could improve your machine performance? Contact us!