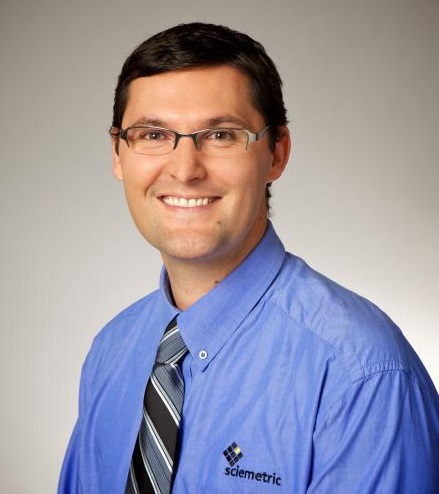
Contributed by: Ron Pawulski - Account Manager
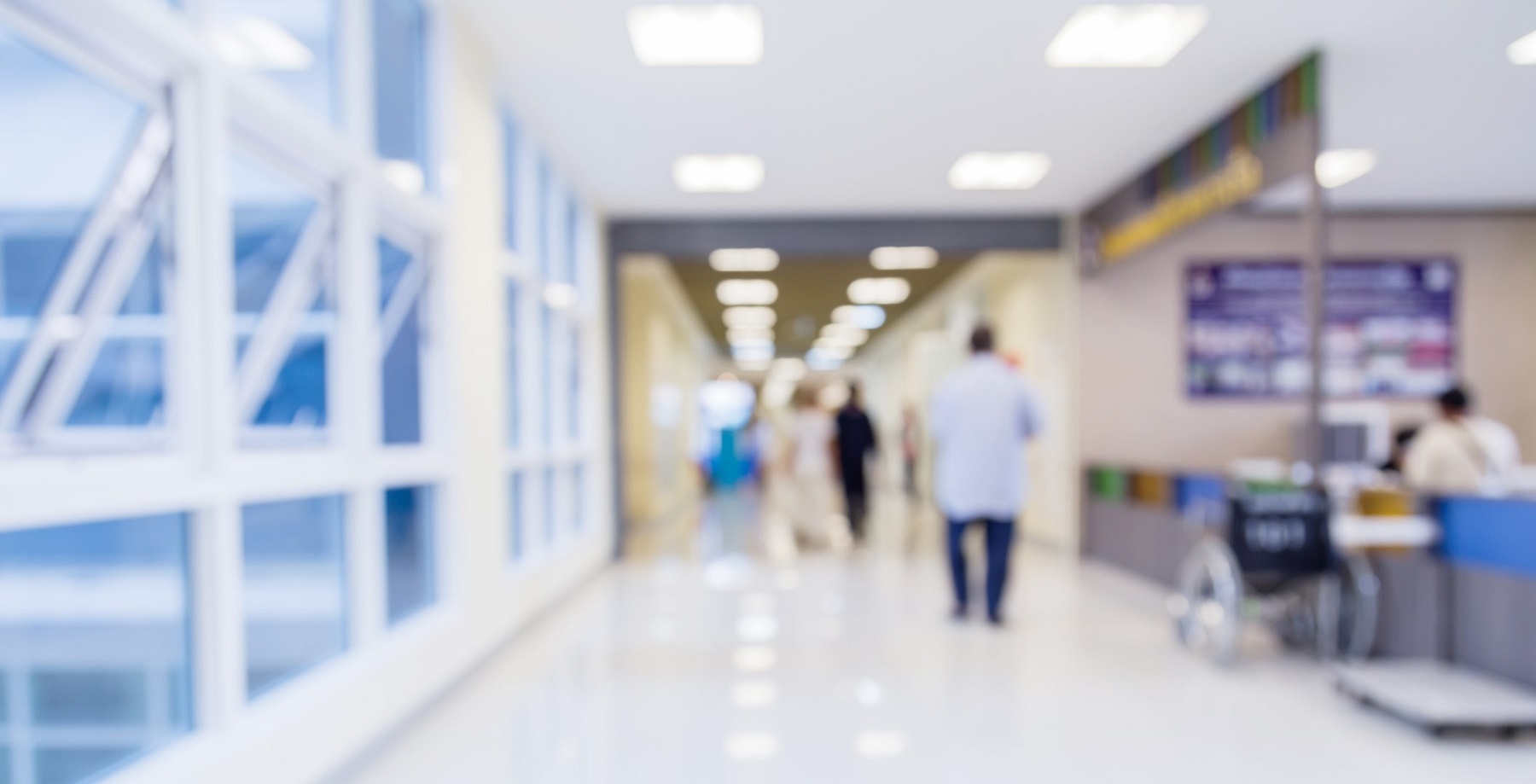
The medical device industry is subject to stringent regulatory oversight in how products are manufactured and shipped. Sterility is key to patient safety. This begins with how devices are packaged and sealed prior to shipping. A failed seal requires the product to be repackaged or even scrapped.
We worked with one maker of implantable cardioverter defibrillators (ICDs) and pacemakers that had significant production disruptions due to problems with its packaging.
These devices are packaged in a hard plastic clamshell, sealed shut with a Tyvek backing. A heated plate presses and adheres the Tyvek to the clamshell. The sealed package is then subjected to a chemical steam bath which penetrates the Tyvek and sterilizes the contents.
For quality control, the manufacturer would pull sample units from each batch at the end of the production line and use two tests. The first measured how much force it took to open the package – too little likely indicated a poor seal. The second used visual microscopic inspection to look for bubbles or breaches in the seal.
Any issue would result in a whole batch being quarantined for further testing. It would also trigger regulatory protocols that could lead to two or three weeks of production downtime – costly, to say the least.
Using in-process testing and signature waveform analysis to ensure quality in medical manufacturing
When the manufacturer started to experience excessive failure rates, it decided to implement in-process testing and signature waveform analysis to catch issues as they occurred. The goal was to have the data trail and traceability to go from a “batch of many” to a “batch of one.”
We added sensors and thermal couplings to monitor the temperature across the surface of the heated plate, the force applied, the angle of the plate as it came down to ensure even contact, and the consistency of the air supply pressure in the pneumatic system that applied the plate since variances here could impact press force and time.
We collected the full digital process signatures for all these variables for every press and sealing operation. This waveform data was then plotted and overlaid using analytics software to spot trends and anomalies, and determine the signature profile of an ideal seal.
The dark red line indicates a good seal, while the others are failures.
Implementing this quality control system allowed the manufacturer to quickly identify the root cause of failures, minimize the impact on production schedules and reduce product rework.
This ultimately saved time and money by reducing the reliance on expensive downstream inspections and achieving high correlation between automated test techniques and visual quality checks.
Want more information?
Click here to find out more information on how we can help with your medical device testing needs. Contact us at inquiries@sciemetric.com to speak with Ron.