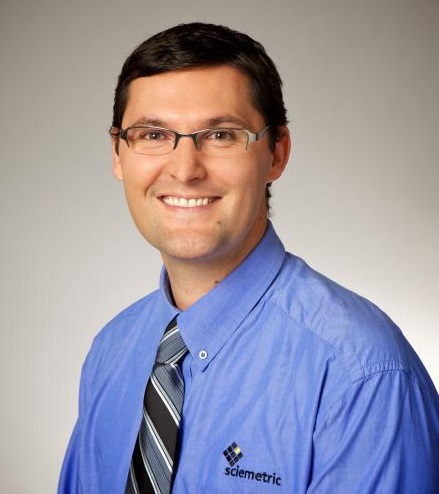
Contributed by: Ron Pawulski - Account Manager
In-process testing and digital waveform analysis isn’t only for discrete manufacturing where each part is serialized. It can also be used to improve yield and quality control in pharmaceutical and medical device batch manufacturing.
Using in-process test and digital waveform analysis to ensure quality when it matters most
We worked with one maker of “Y-site” intravenous (IV) connectors. These are insertion points for additional medication to be added to an IV drip. In the image, the white cap is a needleless valve – a type of screw lock where a syringe locks on with a half turn to dispense medication without using a needle.
This cap is welded to the larger Y piece using ultrasonic welding, which melts the plastic together with the friction generated by vibration.
Like other welding techniques, the variables that can affect weld quality include current, force, distance and voltage. Each weld takes only a few seconds to complete. These components are cranked out in high volume and tracked by a batch ID number, rather than individually serialized.
The welding machine possessed basic capabilities to give a pass/fail on a weld, but it couldn’t collect and store the data from the process. The manufacturer lacked the means to trace root cause and understand why failures were happening. Without that insight, tracking down the reasons for failures resulted in extended downtime and unresolved warranty claims. A common failure was the cap breaking off the Y piece due to a poor weld.
We added sensors to collect the full digital process signature for the current, force, distance and voltage of each weld. This data was combined with other part information, including component manufacturer, batch ID, operator ID and machine fault data, to correlate weld failures to common variables.
This allowed the manufacturer to now trace failures to the right upstream variables. For example, a problem with a batch could now be traced to a specific supplier of caps or Y pieces, suggesting a need for that supplier to improve its quality control processes, or to a specific welding machine, indicating a need for maintenance or repair.
This obviously saved time and money, and gave the manufacturer the insight to answer the “why” question quickly and accurately.
Want more information?
Click here to find out more information on how we can help with your medical device testing needs. Contact us at inquiries@sciemetric.com to speak with Ron.