Contributed by: Sciemetric Staff
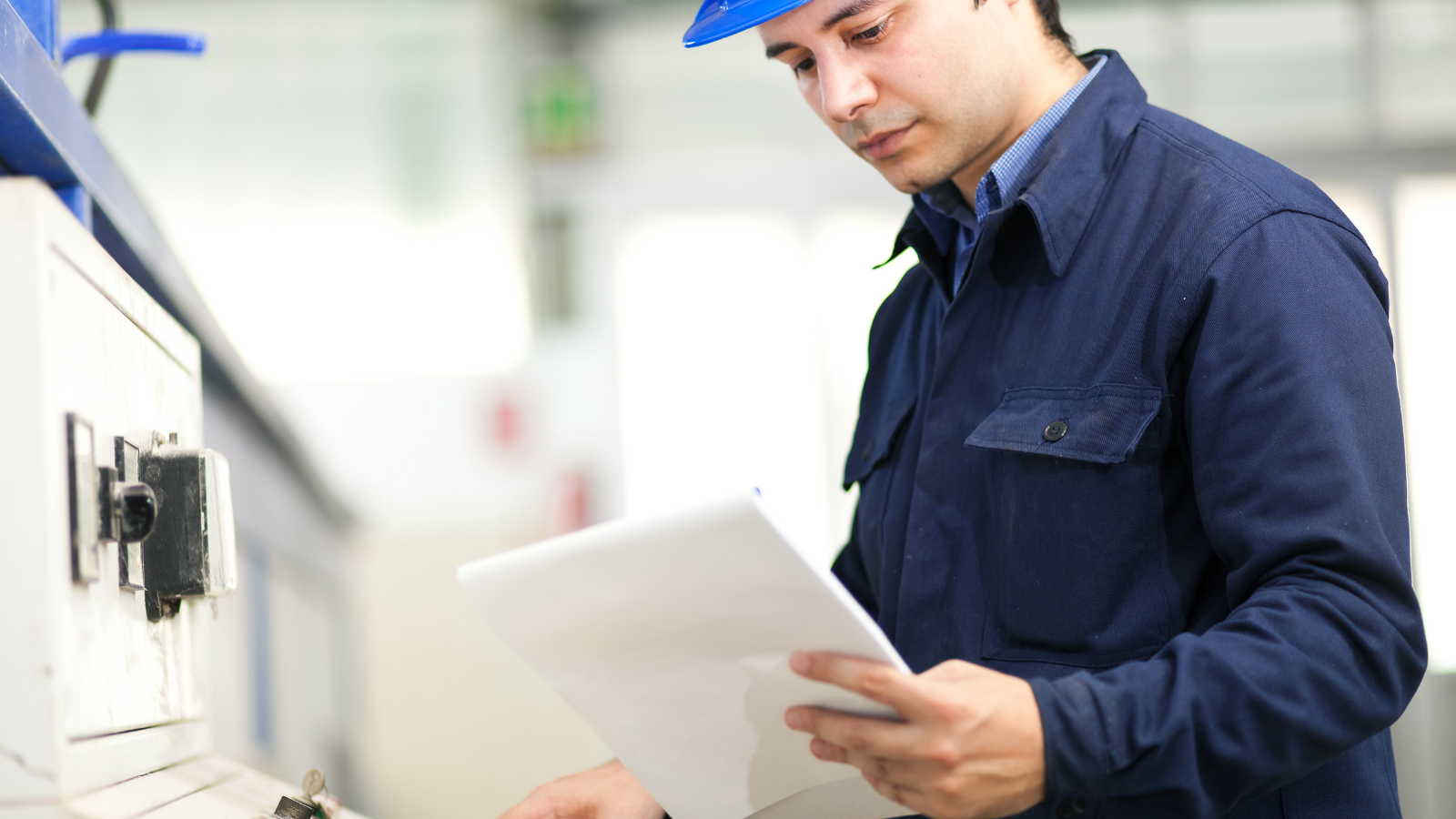
Data is everywhere in manufacturing plants and yet there are gaps in the ability to turn it into actionable information. When it comes to keeping stations running efficiently, maintaining production throughput and meeting first time through (FTT) goals, specialized approaches may be required to enable engineers on the floor to be proactive or respond quickly.
The below 7 questions will help you identify the data gaps that may be holding back the effectiveness and efficiency of your production line.
1.How long does it take to determine the root cause of a quality problem?
If trying to track down the root cause of an issue that has affected quality or productivity takes days or weeks, you may be missing data that would allow you to get to a faster resolution. If only simple pass/fail results are collected and saved from test stations, for example, there will not be enough data to provide a more direct path to an answer.
2.Are you overwhelmed with production data—and is any of it helpful?
Despite understanding the value of production data and making an effort to collect it, many manufacturers are not collecting the right data, and lack the tools to retrieve and analyze their data to quickly trace root cause when quality issues affect production. Consider what the typical goals and challenges are on the line day-to-day and determine what data would be most helpful.
3.Do you have databases scattered across the production floor (and different data types), making it difficult to review your manufacturing data?
Many manufacturers end up with a collection of miscellaneous database systems, either sourced from different vendors or built in-house. Lacking continuity or the tools to parse this data into a standardized format and flow it in real-time into a centralized database makes meaningful analysis nearly impossible. A problem caught at the end-of-line test is much more difficult to trace if the part and process data is not consolidated.
4.Is setting up test limits on your production line a matter of guesswork?
If setting up limits on test stations is left to trial and error, this is a data gap that can be improved on your line. With the right manufacturing analytics, data-derived test limits can be set, not only eliminating the uncertainty and constant tweaking in production, but also enabling a clear balance of quality vs. cycle time.
5.Does your team struggle to optimize test cycle time, while maintaining product quality?
Modern data analytics can mine your archive of stored data, to conduct a range of tests and simulations without having to run additional parts through a process to validate parameters. Review that historic data and run simulations to see where and how a test cycle can be shortened without impacting quality assurance. This boosts productivity and can reduce the number of test stations.
6.How easily can you compare your production data and quickly visualize a problem?
Having a data analytics solution that offers data visualization capabilities can have a huge impact on your ability to do quick, meaningful analysis of your production data. It can be for analyzing lots of serial numbers or to compare performance across parallel stations. For example, using QualityWorX’s data visualization capabilities, it is easy to rapidly compare and overlay hundreds, if not thousands of process signatures (representing data gathered from each test cycle). Quality engineers can then quickly find trends and patterns that reveal the “how” and “why” of decreases in yield, then test and apply refinements to test limits or other upstream quality control benchmarks.
7.Are any of your test stations reporting false passes or false failures?
Repeatability is key to any manufacturing process. The key to mastering it lies with data – you must collect and analyze the part data generated by the system through each test cycle, just as you would for any process on the line.
Having the data means you can identify and exclude all the controllable variables that can impact the test regardless of the equipment – sealing variations, operator behavior, etc. The goal is to determine what the test system is capable of in the absence of all these other external variables. Once you have confidence in your test equipment, you can systematically tackle the controllable variables to improve process.
Enhance how engineers can use manufacturing data for countless improvements on the line
A yes to any of the questions above is a sign that there is a something that could be improved in your plant’s approach to data collection, management and analytics.
Manufacturers can cost-effectively deploy tools that will allow them to bridge this gap and maximize the utility of this data. The goal is to close the gap between the presence of a quality issue, awareness and resolution – something we help manufacturers do using our QualityWorX data management and analytics software suite. Using QualityWorX, you can collect the critical data from your part production processes and analyze this data to make improvements to part quality and overall production on your line, including:
- go beyond pass/fail decision-making; easily make comparisons and set better limits using process data
- solve problems faster; identify the problem and the solution for continuous improvement
- optimize station performance (speed, part quality)
Learn how to use data to improve your production line, including:
- How to look at the production problems you’re experiencing to know if you have a gap between data and insight
- How to turn "Big Data" into better data
- How to apply the right data management and analysis tools and capabilities to make your data work for you
- How we are helping manufacturers bridge the gap between the data they collect and how they use it to drive continuous improvement