Contributed by: Sciemetric Staff
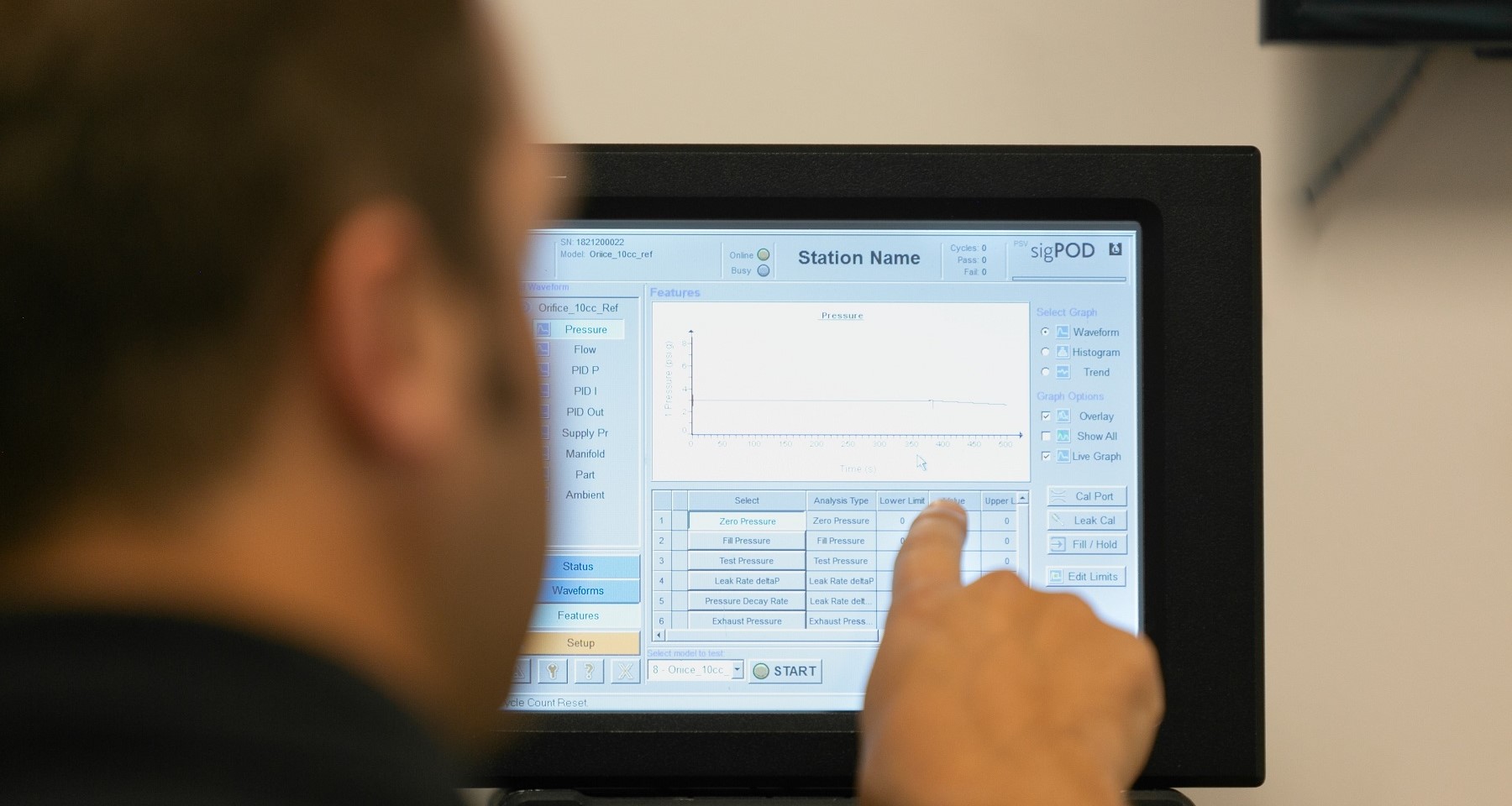
“Industry 4.0” has become a catchall for a host of technologies with the potential to disrupt and digitally transform conventional manufacturing – from blockchain to AI, robotics to augmented reality.
But if the intent of Industry 4.0 is to make factories more efficient, more profitable and generally better at what they do, the starting point should be on how to make the most of the data potential already available to you on the production line.
Are you making the most of your part production data?
Part production data – the data generated by a part in production from each process and test – is an extensive resource which is too often overlooked, underused and under-appreciated, despite the fact that manufacturers are buried in reams of it.
Many manufacturers continue to focus on data collection rather than data utilization. They don't yet have the modern data analytics tools in place that will allow them to squeeze from their part data the actionable insight that is crucial to meeting Industry 4.0 benchmarks they are seeking for quality, yield and traceability.
To use your data more effectively all begins with the digital process signature (sometimes also referred to as waveforms or traces).
A process signature is a visual representation of everything that happened through every millisecond of a manufacturing operation on a particular part. Each combination of a part and a process is unique. With any controlled process – press fitting, leak testing, welding, liquid dispensing and so on – the signature is repeatable and consistent when parts meet specification. A signature that does not match indicates a flawed process and a defective part.
The insight to take immediate action
In-process testing (IPT) using digital process signature analysis provides unparalleled insight at the station level, in production real-time, for each cycle of an process or test. Think of it as a video instant replay, versus the handful of snapshots provided by scalar data alone.
The first generation of technologies to collect and analyze process signatures in this fashion were a proven success on the manufacturing lines of major automotive OEMs in the 1990s. Today’s iteration are even more powerful and cost-effective platforms that can be deployed quickly, to begin generating the actionable insight that can address sticky quality issues before the morning coffee break.
These tools are agnostic, additive and scaleable:
- They can be hooked up to existing process and test equipment from just about any vendor.
- They feature modular designs that can easily scale up.
- They can be plugged into other manufacturing analytics platforms so their signature data can be integrated with other datasets from across the line for deeper and more comprehensive root cause analysis.
What’s around the curve on your production line?
A system like this provides manufacturers with a powerful tool to drive continuous improvement and quality gains, while delivering the traceability their customers and partners have come to demand. These are the metrics that a manufacturer should focus on as the first step of any Industry 4.0 digital transformation initiative.
To learn more about the versatility and utility of digital process signature analysis on the manufacturing line and why it should be considered fundamental to any Industry 4.0 effort, download our latest white paper, What’s Around the Curve? 5 ways a process signature reveals insights from your production line.