LEAK TEST EQUIPMENT FOR MANUFACTURING
Turnkey Leak Test Stations
Sciemetric offers a selection of turnkey leak test stations to allow for quick and easy installation on your production line. The turnkey leak test stations can be easily configured for any test on your line, equipped with high quality sensors and simple calibration processes.
Sentinel 3520
The Sentinel 3520 is equipped with patented leak test technology designed to specifically address the issues faced by manufacturers, delivering supreme accuracy and fast cycle times.
Sentinel Blackbelt Pro
Reliable 4-channel testing, ideal for flow, leak, vacuum, and pressure-decay tests
Sentinel I28
The most advanced single-station air flow and leak detection equipment available today
Sentinel Blackbelt
The best single-station, benchtop leak test instrument available
Sentinel C28WE
Providing fast and repeatable leak test results
LPC 528
Compact instrument specializing in the use of differential pressure decay technology
Sentinel C20WE
The perfect low-cost leak test solution
TracerMate II
Tracer gas management system suited for evacuating and backfilling test parts for sniff testing and tracer gas detection
CTS Connectors
Sciemetric partner company, Cincinnati Test Systems (CTS) offers a full line of pneumatic connectors and seals for your leak testing equipment, including pneumatic tube fittings, Luer connectors, and more. CTS also offers custom leak test connectors for seal surfaces in irregular shapes and sizes.
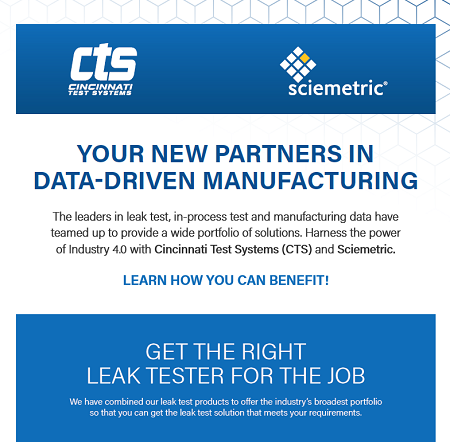
Benefit from the most comprehensive leak test product lineup in the industry
Sciemetric’s partnership with Cincinnati Test Systems (CTS) means that customers gain access to products and support across the industry’s most comprehensive leak test product lineup—including advanced data and analytics capabilities. This partnership offers you the most innovative leak test technology and industry-leading accuracy and reliability, making it the ultimate defect detection and productivity solution for leak test on manufacturing production and assembly lines.
We offer leak testers for small and large volume applications, applying pressure decay, mass flow, vacuum and more. You can rely on the CTS and Sciemetric portfolio of products to catch even the smallest leaks in any part or product where seal integrity is critical.
Get the right leak tester for the job
We can help
No matter the application, our comprehensive leak test lineup has a solution for you. Our leak test experts will help you find the right leak testing equipment for your production line.
We have combined our leak test products to offer the industry’s broadest portfolio so that you always get the leak test solution that does exactly what you need it to do.
Our diverse portfolio offers solutions for every test on your line. With our combined in-depth knowledge of leak testing for a variety of applications and large to small leaks, as well as our thorough expertise in in-process testing, our team is equipped with the knowledge and products to test and monitor virtually any manufacturing process on your production line.
- Leak Testing
- Sound & Vibration Analysis (NVH)
- Torque Monitoring
- Weld Monitoring
- Process Monitoring
- Functional Testing
- Press-Fit Monitoring
With over 110+ combined years in business, no one has walked more lines than our combined team. We have worked on over 30,000+ systems worldwide, solving quality and productivity problems for thousands of manufacturers across the globe. Equipped with some of the best engineering talent in the market, our dedicated team of support and applications staff is here to serve you.
Experience across a variety of industries:
- Automotive
- Off-highway
- Oil and gas
- Medical devices
- Consumer products
- Energy
At Sciemetric and Cincinnati Test Systems (CTS), we work to provide you with solutions that solve your problems and help you meet your quality and productivity goals. We know that you need to meet your cycle time and throughput targets, while accurately and reliably testing each part of each component on your line. We also know that you need the ability to trace root cause and access detailed birth histories for each part and assembly on the line. All the while, staying on budget.
We understand the demands and pain points of the production line and no matter your problem, we’ve got a solution to meet your needs.
With our combined team, Sciemetric and Cincinnati Test Systems (CTS) have you covered across the globe better than ever before. We offer sales and service in the following regions, as well as extended coverage wherever you need it.
- USA (Rochester Hills, MI; Harrison, OH)
- Canada (Ottawa, ON; Windsor, ON)
- Mexico
- South America
- Caribbean
- UK
- Europe
- India
- China
- Korea
- Australia
Solutions for every leak test on your production line
The diverse portfolio offered by Sciemetric and Cincinnati Test Systems (CTS) provides leading testing, monitoring and data analytics solutions for every leak test on your line. We offer pressure decay leak testing and vacuum decay leak testing, including pressure drop measurement and calibrated leak rate measurement. We offer flow testing, including leak testing, blockage testing, burst testing and functional flow measurement. We also offer tracer gas testing for helium (evacuate and fill test), hydrogen, and other gases, as well as tracer gas testing for hard vacuum, accumulation and atmospheric at point of leak (sniffing and purged containment).
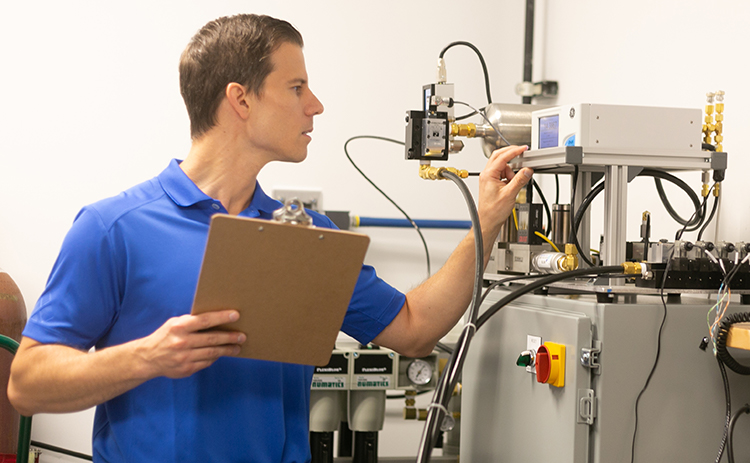
Improve your leak test: Proven results
Our leak test customers have experienced many benefits, including:
- Improved leak test accuracy and speed, significantly reducing gage R&R
- Improved efficiency and reduced costs by bringing leak test in-line
- Improved cycle time to reduce the number of leak test stations required on their production line
- Reduced repair costs and warranty claims by improving leak test detection and accuracy
- Achieved an average return on investment within 4-6 months