Contributed by: Sciemetric Staff
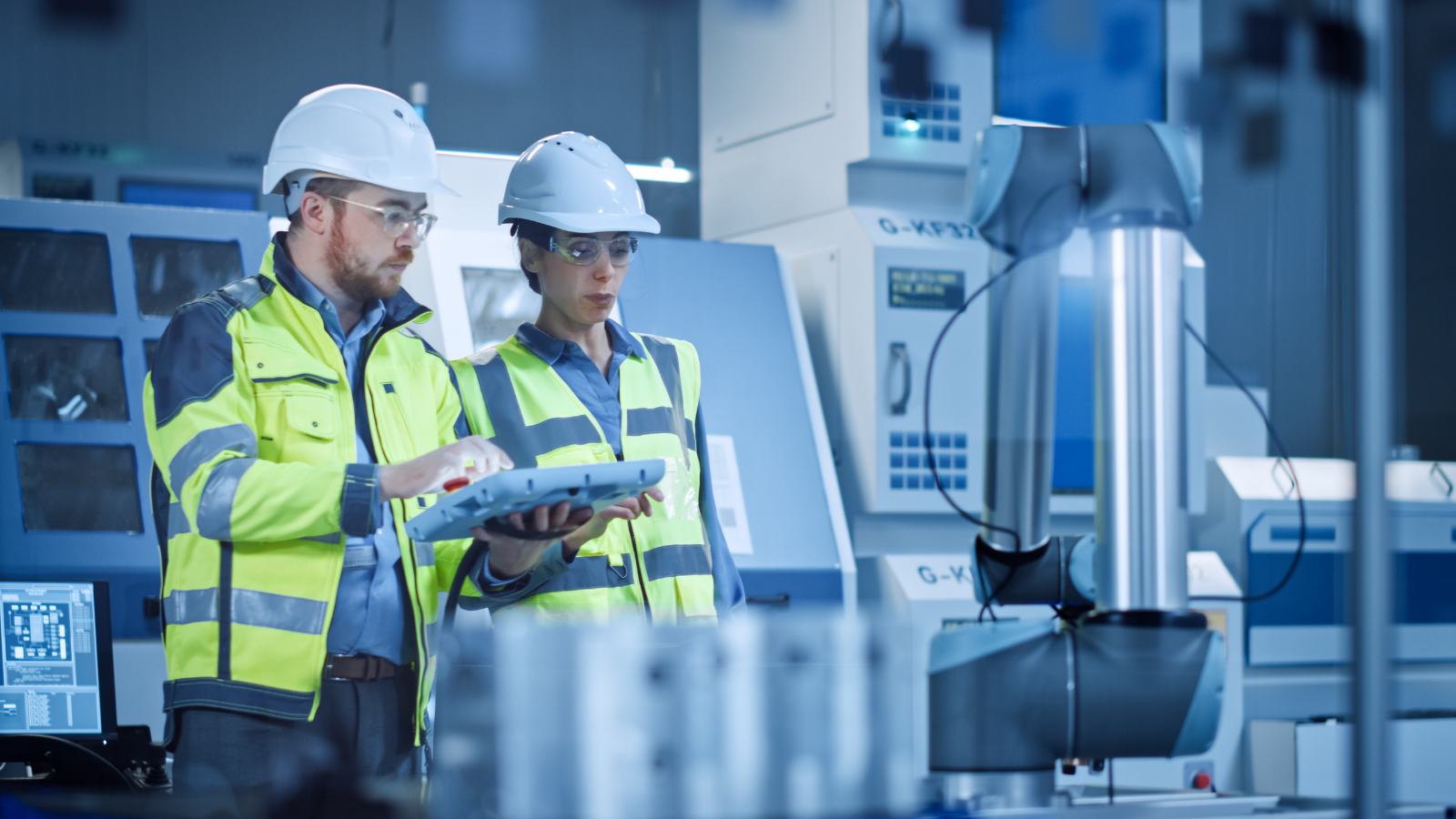
Manufacturers across all industries are being challenged to reconsider what they do and how they do it. On the production line, it’s all about reaching higher levels of product quality and efficiency.
But this doesn’t mean you have to engage in a costly rip-and-replace of legacy equipment. We continue to see the greatest value in making the most of what you already have.
Below, we share 5 tips to consider as you work to improve your production line efficiency, and product quality.
1. Start with a hard look at First Time Yield (FTY)
The more stations there are on a line, the greater the need for a data-driven quality assurance process that can ensure the FTY at each station is as close as possible to 100%.
For example, consider a line that has 50 stations in series and each station operating, on average, with an FTY of 99%.
That 99% may sound high, but by the end of the line, the Rolling Throughput Yield, or RTY, is only about 60%. The result is a scrap or rework rate of 40%. That will cost you—a lot.
2. Detect defects where, and when, they start
The closer to its point of origin that you detect and define a production flaw that is impacting FTY, the less disruptive it will be to overall production, and the less costly it will be to fix.
And yet, many lines continue to rely on test, inspection and quality control methods that push defect detection downstream. Why continue to put time, money and materials into a part or sub-assembly that may have to be scrapped?
That’s not to say that end-of-line or other downstream testing don’t have their place. But again, for overall quality gains, your team’s focus must be on more than just a final quality check. Instead, consider what checks and balances can, and should, be instituted at every critical juncture as a part or assembly progresses down the line.
We call this in-process testing.
Learn more about why relying on end-of-line testing is bad for your bottom line >
3. Gain real value from your part production data
With the above points in mind, the next logical question is what do when a defect is detected, or a part fails a quality check.
Simple—find out why, by collecting and analyzing the right data.
Take, for example, a part that has failed a leak test. At previous stations, this part has been drilled and clamped, and was subject to a dispensing operation and a weld. A flaw with any one, or more, of these processes could be responsible for that leak test fail.
With the right sensors and software, existing process stations on the line can be equipped with the intelligence tools to collect, correlate and visualize the highly granular part production data that is generated by the part, not the machine, during a process or test cycle.
This enables you to consider the problem from the perspective of the part instead of just looking at the station for more effective, actionable insights.
4. Set yourself up for success with the right data
So, just what is part production data?
At Sciemetric, we provide the full digital process signature, or trace, of each process or test cycle, from anywhere on the line. We like to think of a signature as similar to an ECG. It captures and visualizes what happened through every millisecond of a process or test.
With this granularity, it’s easy to cut through the noise and develop feature checks (with corresponding limits) for every way that any process or test can go wrong. For example, the relationships between time, force, distance, pressure or voltage. This data can be further correlated with machine vision inspection images and data for even deeper insight.
Learn more about the kind of data you should be collecting on your production line >
5. Unlocking the power of your production data doesn’t have to be complicated or costly
What we have described does not require a costly rip and replace of existing technology.
No. The means to collect and analyze part production data involves additive technologies. Your team can realize more value, more efficiency and greater productivity from existing equipment, by collecting the right data and breaking down any existing data silos across the plant floor that may be impeding quality gains.
We find that the best software solutions for defect detection on the line emphasize commonality – what we call the “5 Cs” – common hardware, common software, common look and feel, common learning curve and common spare parts. This one system/technology platform can be used across the assembly line to evaluate and improve various processes, with a standard universal hardware and software interface.
Why wait to benefit from proven digital intelligence on your production line?
Make your existing production line investments work, not just harder, but smarter. This is the priority for 2022. The good news is that the production technologies which your plant needs are already available and proven. Best of all, they are designed to augment, not replace, your existing investments. Contact us to learn more.